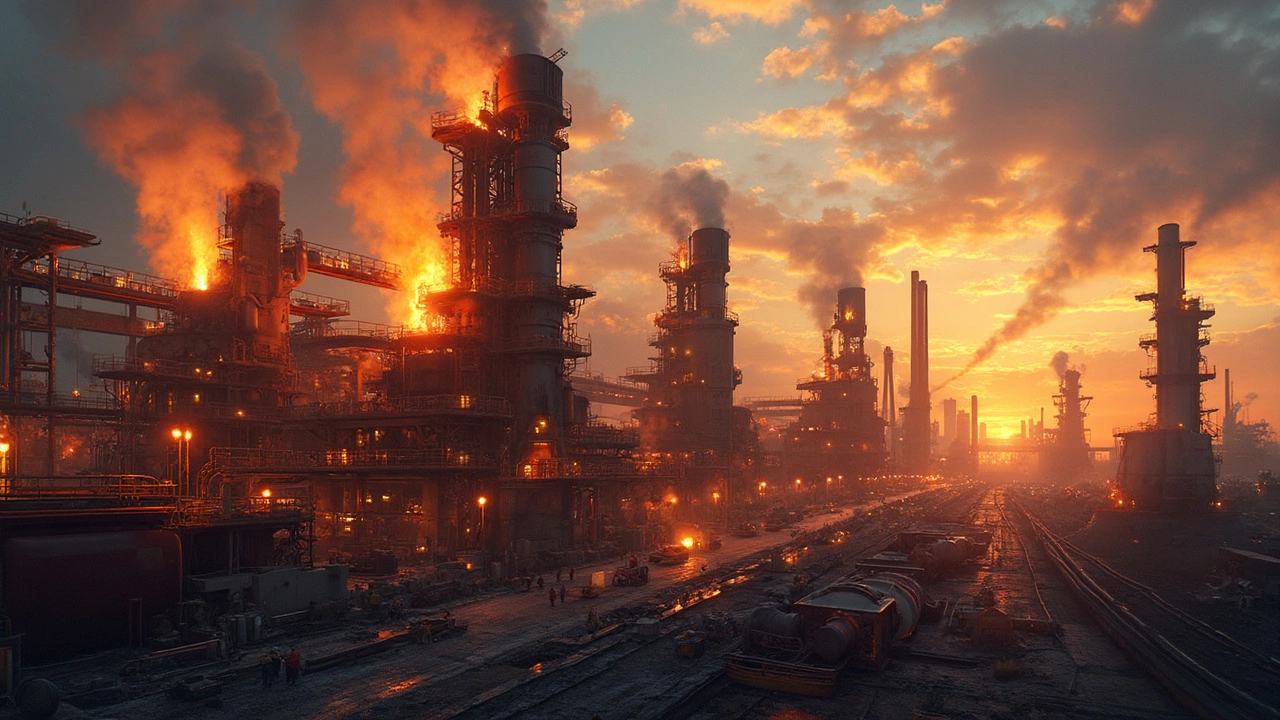
Most people think steel plants in the US are some relic from the past—dusty, closed factories with smokestacks that stopped working decades ago. But if you take a look today, the American steel industry is alive and kicking. New mills keep popping up, old plants upgrade with cutting-edge tech, and the whole sector works around the clock.
Curious about where to find these factories? You'll run across steel plants in places like Indiana and Ohio, but also in spots you might not expect, like Alabama and Arkansas. Mini-mills, which are smaller and more high-tech, have been showing up near large cities and major highways. These locations aren't random—they pop up close to where steel is needed most or where shipping is easy.
If you're thinking about how this industry affects daily life, just look around you. Bridges, cars, kitchen appliances, and even canned food rely on American steel. Knowing where these plants are and who runs them can really help if you're hunting for suppliers, thinking about a career switch, or just want to understand what keeps American infrastructure running.
- Where the Steel Plants Are Now
- Big Players and Emerging Names
- What These Plants Actually Make
- Why US Steel Manufacturing Still Matters
- Tips for Finding Steel Suppliers or Jobs
Where the Steel Plants Are Now
If you want to know where steel manufacturing is still big in the US, start by looking right in the country's heartland. States like Indiana, Ohio, and Pennsylvania have always been major players, and they're still leading the way. For example, Indiana has more steel jobs than any other state. The city of Gary alone is a huge hub, home to the sprawling U.S. Steel Gary Works, which is one of North America’s largest steel manufacturing plants.
But it's not just about the Rust Belt anymore. Newer plants, especially those known as ‘mini-mills,’ are making waves in the South. Take Nucor, one of the biggest names in the US steel plants game—they’ve got massive operations in places like Arkansas and South Carolina. These mini-mills recycle scrap instead of starting from iron ore, so they’re popping up where there’s easy access to scrap and major highways. It’s all about saving on transportation and staying efficient.
State | Major Steel Plants |
---|---|
Indiana | U.S. Steel Gary Works, ArcelorMittal (now Cleveland-Cliffs) Burns Harbor |
Ohio | AK Steel (now Cleveland-Cliffs) Middletown, Nucor Marion |
Arkansas | Nucor Hickman, Big River Steel |
Alabama | AM/NS Calvert, U.S. Steel Fairfield Works |
Texas | Steel Dynamics, CMC Steel Texas |
Don’t picture just giant old factories, though. Some of the newest steel factories are high-tech spaces running round the clock. Out west, Utah and Colorado both host plants that mostly serve local construction and manufacturing. Even in California, there are mills—though those tend to focus on more specialized steel products.
So, if you thought American steel was fading away, it's actually spread out across the map and more active than most people realize. The spots with strong shipping routes, access to scrap, and industry demand are exactly where you’ll find the action in steel production USA today.
Big Players and Emerging Names
If you picture US steel plants, you probably think of big names like U.S. Steel or Cleveland-Cliffs. These heavyweights still lead the pack. U.S. Steel has been around since 1901, and it's still got huge plants, including the Gary Works in Indiana—one of the largest steel manufacturing sites in North America. Cleveland-Cliffs isn’t far behind; it scooped up AK Steel and several other producers in recent years, cementing its spot as a major force.
Nucor is another giant changing how American steel is made. They run dozens of steel factories scattered across the country, mostly focusing on electric arc furnaces, which recycle scrap metal. This method is cleaner and quicker, and it pushed Nucor past old-school competitors in terms of raw output. To give you an idea of scale, Nucor pumped out almost 22 million tons of steel in 2023 alone.
But it’s not just about the familiar names. Keep an eye out for newer and growing firms like Steel Dynamics and Big River Steel. Steel Dynamics has invested big in modern steel production USA, especially in the Midwest. Big River Steel, which started in Arkansas, uses high-tech processes and now operates under the U.S. Steel umbrella, bringing new ideas to an old industry.
Company | Main Locations | 2023 Output (Million Tons) |
---|---|---|
U.S. Steel | Indiana, Pennsylvania, Alabama | 16.5 |
Nucor | South Carolina, Arkansas, Texas | 21.8 |
Cleveland-Cliffs | Ohio, Indiana, Michigan | 16.2 |
Steel Dynamics | Indiana, Texas, Mississippi | 13.1 |
For smaller or regional operations, mini-mills are popping up in states like Alabama and Oklahoma. These places aren’t looking to make headlines—they just focus on serving local builders and manufacturers who want reliable American-made steel.
So if you're tracking the American steel industry, it’s not just about a few huge companies anymore. Modern tech lets smaller players get a foot in the door, and even the old giants have to keep evolving to keep up.
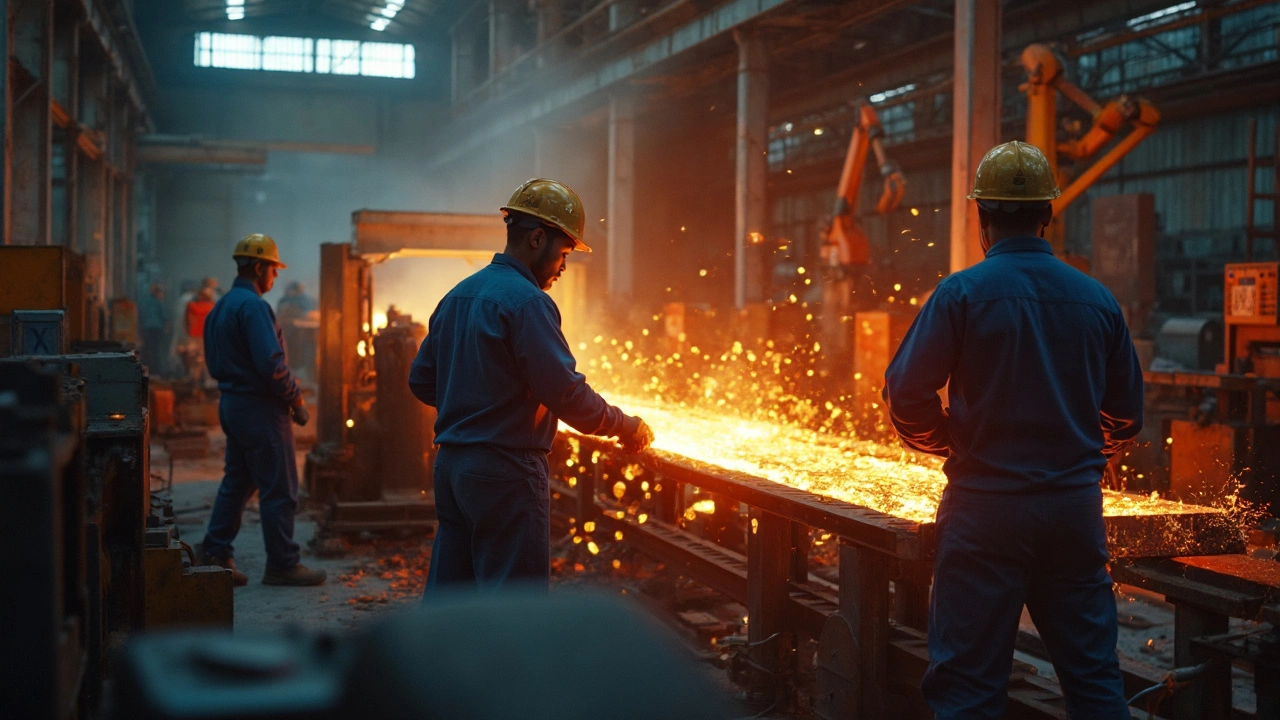
What These Plants Actually Make
So, what rolls out of those big doors at steel manufacturing plants in the US? It’s a lot more than just huge sheets of metal or smokestack drama from old movies. American steel industry plants today crank out countless products, each serving a real purpose in modern life.
The heavy hitters are steel coils and sheets, which get sliced and shaped into everything from car bodies to roofing panels. Pipes and tubes are a big deal too—they run through oil fields, water systems, and even the skeletons of skyscrapers. Next up are the beams and bars, known as rebar and structural shapes, that hold up everything from apartment buildings to highway bridges.
Let’s get specific. Here’s a quick rundown of the most common products you’ll find leaving US steel plants:
- Hot-rolled and cold-rolled sheets: The backbone for cars, fridges, washing machines, and metal roofs.
- Rebar and beams: Essential for construction—think highways, commercial buildings, sports stadiums.
- Pipes and tubes: Used in construction, plumbing, oil and gas, and even playground equipment.
- Wire rod and mesh: Goes into fencing, concrete reinforcement, and making nails or screws.
- Specialty steels: These are tailored for things like medical tools, military vehicles, or wind turbines.
Most big plants (like the ones in Indiana or Pennsylvania) specialize in what’s called “integrated” steel production, going from raw iron ore all the way to finished steel. Newer mini-mills, on the other hand, mostly recycle scrap metal into high-quality steel—it’s faster and causes less pollution.
Just to put numbers on it: In 2023, American steel mills produced about 80 million tons of steel. Roughly 70% of that came from electric arc furnaces (mini-mills), showing how recycling and newer tech are overtaking old blast furnaces.
Product | Main Uses |
---|---|
Hot-rolled coil | Building, automotive, shipbuilding |
Rebar | Concrete construction, roads, parking garages |
Pipes & Tubes | Oil, gas, water transport |
Wire rod | Fencing, springs, cables, nails |
Structural beams | Bridges, buildings, towers |
So whether you’re driving across a bridge, opening a can, or walking through a sports arena, there’s a good chance it wouldn’t exist without something made in a US steel manufacturing plant.
Why US Steel Manufacturing Still Matters
It's easy to overlook steel manufacturing in the US. Most people just assume their car, fridge, or even the beams in their office come from somewhere else. But here’s the thing—American steel manufacturing plants are still crucial for everything we build and use every day.
First, let's talk about jobs. The American steel industry directly supports over 140,000 workers, not counting all the folks in trucking, mining, and equipment companies that rely on steel orders. That makes a big impact in cities like Pittsburgh, Gary, and Cleveland, where entire communities depend on these paychecks.
Then there’s national security. The US military needs steady, reliable access to strong, high-quality steel. If we counted on imports for everything, supply slowdowns or political problems overseas could throw off everything from shipbuilding to bridge repairs. The Department of Defense has even called US steel a "critical national asset." Check this out:
"A strong domestic steel industry is essential for the nation's economic security and defense. Relying too much on imports leaves us vulnerable to interruptions in supply." – U.S. Department of Commerce, 2023
Homegrown steel production USA also helps with disaster response and infrastructure. Need to repair a highway after a hurricane or tornado? Factories in the US can ramp up quickly, while overseas shipping could take weeks or months.
On top of that, American steel factories have made real progress on the environmental side. Many use scrap metal as their main ingredient and lean on electric arc furnaces, which waste less energy than old-school methods. That means less pollution compared to much of the global competition.
Year | U.S. Steel Production (million tons) | U.S. Steel Workforce |
---|---|---|
2010 | 80.5 | ~150,000 |
2023 | 86.0 | ~140,000 |
Bottom line: When you see a shiny new bridge, high-rise, or even a pick-up truck, there’s a good chance it started as American-made steel. Keeping US steel plants strong helps keep the whole country moving forward.
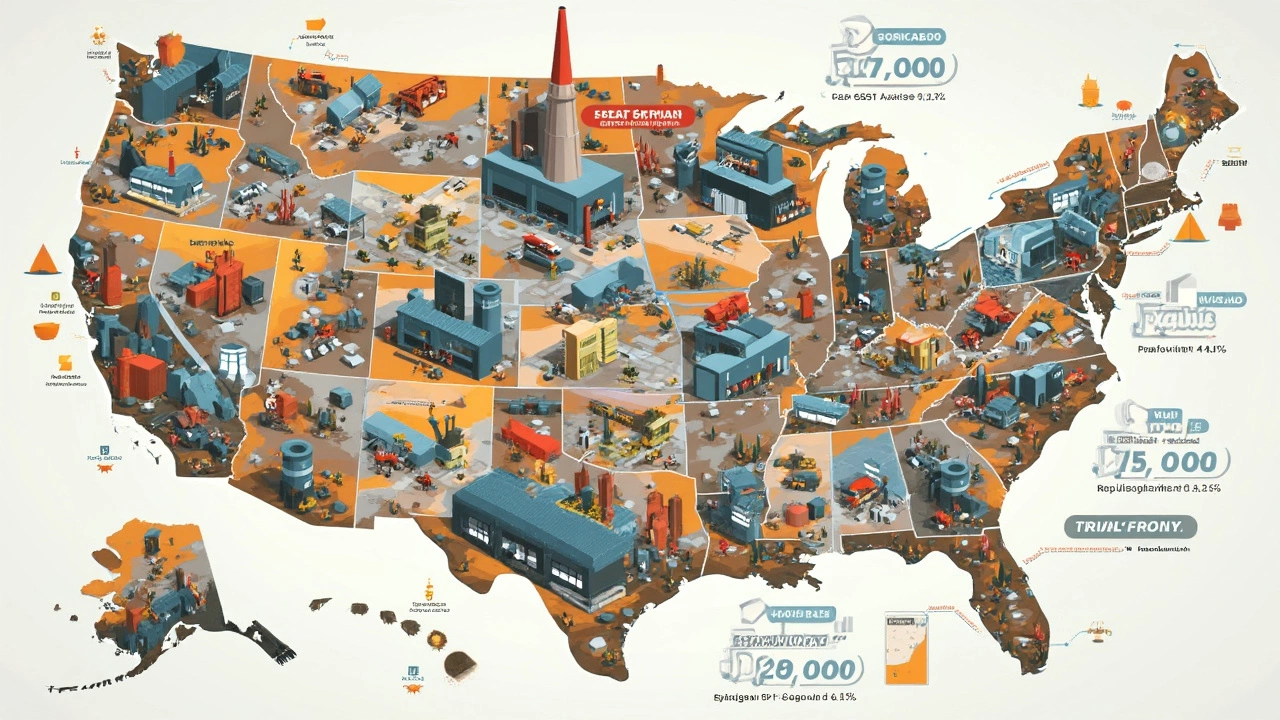
Tips for Finding Steel Suppliers or Jobs
If you want to connect with a steel manufacturing plant in the US—either to buy steel or to snag a job—the process isn’t as tricky as it seems. Here’s what works right now:
- Start your search online. Big names like Nucor, U.S. Steel, Cleveland-Cliffs, and Steel Dynamics have their own websites packed with contact info, job postings, and supply chain details. Type in “steel manufacturing jobs” or “steel suppliers near me” and let Google or LinkedIn do the heavy lifting.
- Check industry directories. The Steel Manufacturers Association (SMA) and the American Iron and Steel Institute (AISI) both keep updated lists of members by region and specialization. These are goldmines for finding everything from rolled coils to specialty alloys.
- Go straight to the source. Many mini-mills take direct orders, especially if you’re buying in bulk. For smaller batches, reach out to steel service centers—places that stock steel from big plants and sell it by the pound or ton.
- Networking pays off. Trade shows like the AISTech Conference or FABTECH in Chicago let you meet hiring managers and suppliers face-to-face. Seriously, a quick chat at a booth can score you a job lead or supplier contact faster than endless email chains.
- Watch for apprenticeship and training programs. Most big steel manufacturing plants offer trainee spots with good pay, benefits, and a steady career path. It’s a solid move if you want job security and hands-on experience.
Wondering about pay scales? Check out this useful comparison:
Role | Average Hourly Wage (2024) | Top States |
---|---|---|
Production Worker | $22.50 | Indiana, Ohio, Pennsylvania |
Skilled Technician | $29.20 | Arkansas, Alabama, Illinois |
Engineer | $38.60 | Texas, Michigan, Wisconsin |
If you want a steady supplier for manufacturing or construction, don’t forget to check order minimums, delivery costs, and payment terms before you lock things in. For job hunters, keep an eye out for union benefits and paid training—both are pretty common in the US steel plants sector and can make a big difference in your earning potential.