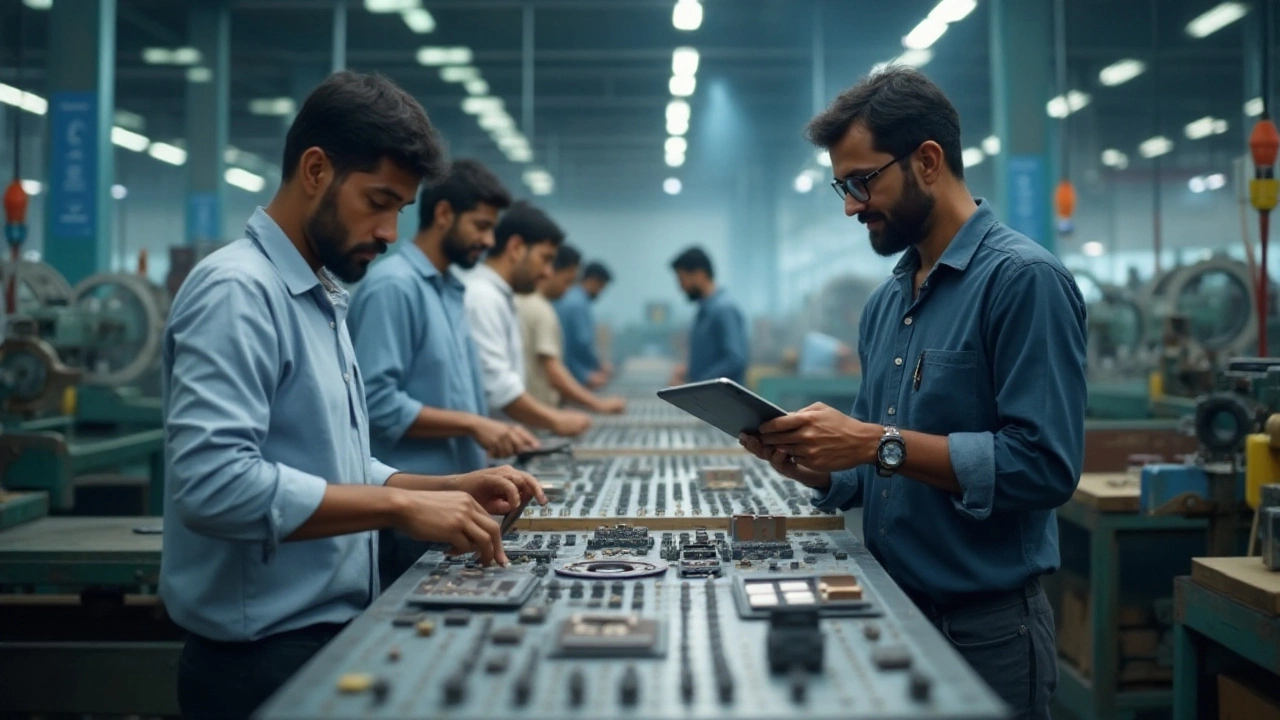
The world of manufacturing often revolves around efficiency and cost-effectiveness. Comprehensive strategies can lead to significant breakthroughs for those setting out in the industry or scaling their operations. One such strategy is encapsulated in the Tim Woods theory.
Originating from lean manufacturing principles, this theory categorizes the typical grounds of waste found in production environments. By identifying these areas, businesses can streamline processes and eliminate unnecessary steps that drain time and resources.
As we explore this theory and its applications, you'll find actionable tips that can make a real difference in the bottom line of manufacturing startups. The opportunity for innovation and restructuring is ripe for those ready to dive into the essentials of production waste reduction.
- Understanding the Tim Woods Theory
- Identifying the Eight Wastes
- Implementing the Theory in Startups
- Benefits of Reducing Waste
- Practical Tips for Success
Understanding the Tim Woods Theory
Diving into the world of lean management and operational excellence, the Tim Woods theory represents a significant concept that any manufacturing startup should delve into. This theory stems from the principles of lean manufacturing developed by Taiichi Ohno at Toyota, with a keen focus on efficiency and waste reduction. The theory itself is structured around acutely understanding and minimizing the eight types of waste commonly encountered in manufacturing environments, known as 'TIM WOODS'. Here, 'TIM WOODS' is an acronym representing eight forms of non-value-adding activities: Transport, Inventory, Motion, Waiting, Overproduction, Overprocessing, Defects, and Skills misuse. Each segment of waste lends itself to unique challenges and requires different strategies for elimination.
Transport waste refers to the unnecessary movement of products or materials during the manufacturing process. It might manifest in the form of extra handling or longer transportation distances which, naturally, extend process lead times and occupy resources without adding value. Inventory waste aligns closely with issues of surplus, where raw materials, work-in-progress, or finished goods exceed demand. Excessive inventory incurs carrying costs, sometimes even becoming obsolete, leading to financial drains. Motion waste is observed in the unnecessary movements of employees which could result in fatigue or inefficiencies, counter-productive to optimal labor utilization.
Waiting, a familiar bottleneck in processes, occurs when there are idle periods due to supply chain delays or machine downtime. Overproduction sees more products or components made than what is required for current demand, tying up valuable resources. Closely tied with overproduction, overprocessing waste is characterized by adding steps or features that are not essential to the customer, leading to inflated costs. Defect waste needs little introduction; it is blatantly the production of faulty goods, which necessitates rework, return, or scrappage, directly impacting profitability. Skills misuse, perhaps less obvious but equally critical, occurs when businesses underutilize or misplace talent, wasting potential creativity and innovation within their own teams.
Why the Tim Woods Theory is Vital for Startups
For startups, understanding the Tim Woods theory is crucial due to the overarching need to utilize resources judiciously. Many emerging enterprises operate with limited capital and tight budgets where waste can spell dire consequences. By identifying and addressing each type of waste outlined by this theory, startups can achieve enhanced productivity, speed up processes, and bring down expenses dramatically. The emphasis is not just on cutting costs but on fostering a culture of continuous improvement and strategic deployment of resources, allowing startups to stay competitive against established industry giants. As Taiichi Ohno once said,
"All we are doing is looking at the timeline from the moment the customer gives us an order to the point when we collect the cash. And we are reducing that timeline by removing the non-value-added wastes."These words beautifully encapsulate the spirit of lean manufacturing, highlighting genuine value creation against a backdrop of relentless and effective waste reduction.
Identifying the Eight Wastes
Embedded within the Tim Woods theory, the identification of the eight wastes offers a powerful lens to view inefficiencies within manufacturing processes. These wastes are not always apparent, yet they silently siphon resources and theoretical profits from businesses. Uncovering and addressing these areas can transform operational life cycles and set a new tempo for productivity.
The first waste is often categorized as transportation. This entails the unnecessary movement of products between stages in the supply chain. Whether through poor layout planning or inefficient processes, minimizing this waste can significantly cut costs. Consider a factory floor where raw materials travel long distances unnecessarily, leading to delays and increased costs. Addressing this requires a strategic review of layout flow, often yielding quicker turnaround times and lower expenditure.
The second waste is inventory, which refers to surplus stock that doesn't immediately contribute to fulfilling customer demands. It's a common pitfall for startups in the manufacturing sector to over-produce, tying up capital in unsold goods. This can be tackled by implementing inventory control systems that better predict demand, leveraging data analytics to adjust production schedules in real-time.
Motion is the third form of waste and relates to unnecessary movements by people or machinery within the production area. The time taken for workers to walk between distant workstations can add up, leading to fatigue and reduced efficiency. Solutions might involve redesigning workspaces or employing automation to handle repetitive tasks more efficiently.
Waiting is another significant waste in the manufacturing process. Idle time, where workers or machines are on standby due to process delays or lack of material inputs, can cripple productivity. By closely examining each step in the production line, businesses can identify bottlenecks and streamline operations using techniques like Just-in-Time (JIT) production, ensuring materials arrive precisely when needed.
"Eliminating waste is the first step toward continuous improvement." - Toyota Production System Principle
The fifth waste is overproduction, often driven by the fear of shortages. However, producing beyond demand results in surplus inventory and increased storage costs. Lean manufacturing techniques such as Kanban can be instrumental in smoothing out production to meet actual demand accurately.
The sixth identified waste is over-processing, or doing more work than is necessary. It includes adding features that customers neither need nor want. Paring processes down to essential tasks through regular assessment helps in eliminating this excess.
Defects represent another form of waste. It is at this stage where errors in production, leading to rework or scrap, are encountered. Instituting rigorous quality control measures and encouraging a culture of accuracy can help minimize this waste.
Finally, unused talent is a critical waste, especially prevalent in startups where agility and creativity are driving success. Failing to utilize team skills locks potential. Encouraging input from all levels can spark innovation and provide fresh perspectives to problem-solving, fostering a more engaged workforce.
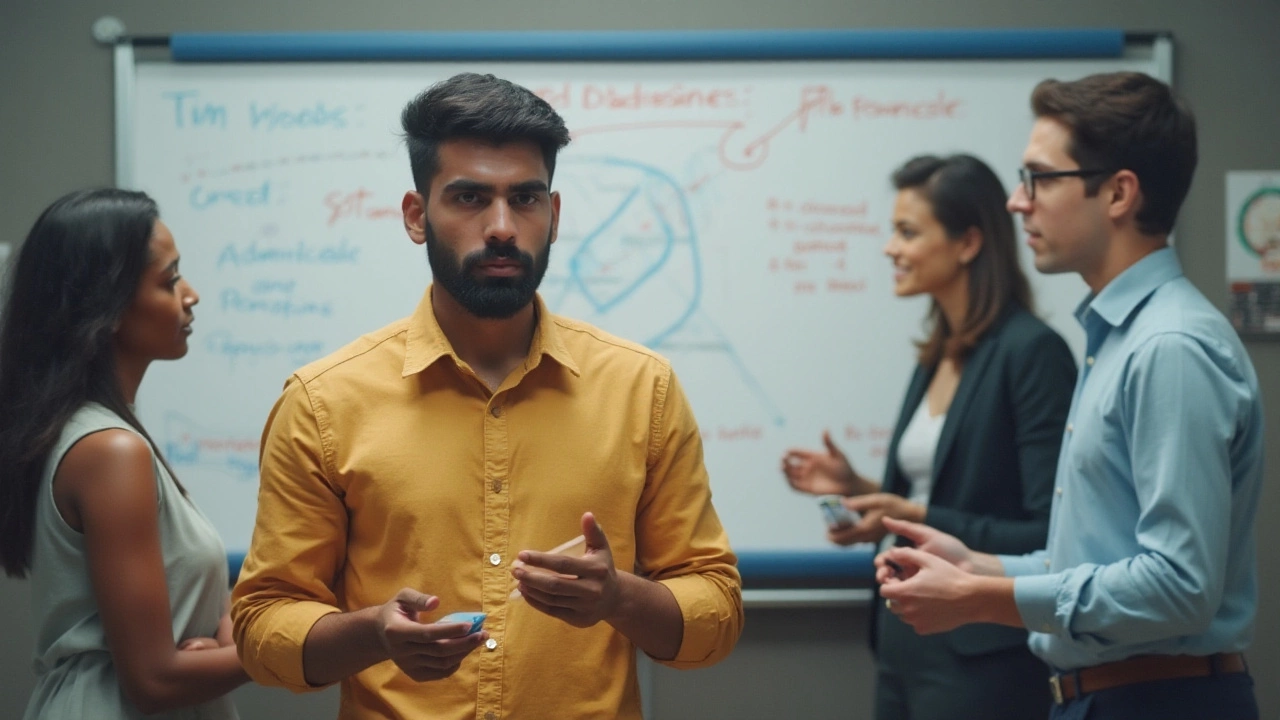
Implementing the Theory in Startups
In the vibrant realm of manufacturing startups, the Tim Woods theory stands as a beacon of operational efficiency. Implementing this theory requires a blend of strategic insight and practical execution. The first step involves an in-depth analysis of current production processes. Founders must channel their inner detective, examining every corner of their workflow to uncover the eight wastes identified in the theory. These include Transport, Inventory, Motion, Waiting, Overproduction, Overprocessing, Defects, and Skills. By isolating these elements, a startup can start tackling inefficiencies and enhancing productivity.
Engaging the team in this initiative is crucial. Employees often possess intimate knowledge of the areas where waste thrives. Holding brainstorming sessions can reveal unexpected insights, enabling teams to collectively outline a blueprint for waste reduction. Once the problem areas have been outlined, they should be categorized based on their impact. This is where prioritization comes into play, as it is crucial to focus on the most detrimental inefficiencies first before moving onto lesser issues.
Leveraging Technology and Innovation
For modern startups, the integration of technology can be a game changer in implementing the Tim Woods theory. Many have explored automation and data analytics to streamline processes. By employing systems that track and report real-time data, manufacturers can gain a newfound visibility over their operations. A startup can, for instance, use smart sensors to monitor equipment downtime, thereby addressing the 'Waiting' wastage. An automated inventory system helps avoid excess stock, solving both Inventory and Overprocessing issues simultaneously.
Balancing innovation and practicality is essential. David J. Anderson, a renowned lean guru, once said,
"Improve the process by engaging those who work in it."This quote highlights the value of integrating both technology and human input. It's a reminder that startups should not forsake the creative human element in pursuit of technological perfection.
- Start by gathering a committed team to pioneer waste identification.
- Conduct a thorough review of production processes to pinpoint inefficiencies.
- Adopt technology solutions that address specific waste categories.
- Ensure continuous improvement by setting regular review checkpoints.
- Cultivate a company culture that values lean principles.
The journey of implementing the Tim Woods theory is an ongoing process of evolution and refinement. Startups that embed this philosophy into their core will not only improve efficiency but also build a resilient framework capable of weathering the competitive marketplace pressures. Equipped with this knowledge, founders can navigate the rocky path of manufacturing with more confidence and foresight.
Benefits of Reducing Waste
When a manufacturing startup embraces the Tim Woods theory diligently, the benefits of waste reduction can be astonishingly transformative. Every piece of waste trimmed from the process not only smoothens operations but also contributes immense savings in terms of both time and money. Imagine an assembly line punctuated with unnecessary delays. By eliminating these obstructions, businesses can increase throughput, turning over more products in less time. Enhanced efficiency not only pumps up production but also accelerates the market delivery, giving startups a competitive edge. This timely readiness meets the consumer demands more accurately and proactively.
Another remarkable impact of reducing waste is rooted in cost management. Consider the resources tied up in overproduction or the costs incurred in correcting defects. Identifying and minimizing such waste through Tim Woods theory can lead to substantial cost savings. Businesses then have more flexibility to allocate those funds towards innovation or expansion. In fact, by conserving resources, startups can invest in research and development, creating more refined and advanced product lines to stay ahead in the market.
Beyond financial benefits, waste reduction contributes to a positive environmental impact. Manufacturing processes often leave significant carbon footprints, but addressing inefficiencies can lead to eco-friendlier practices. This not only enhances the startup's reputation, appealing to conscientious consumers, but can also align the brand with global sustainability goals. Many governments and consumers alike prioritize environmentally responsible companies, so a reduction in manufacturing waste can serve as an outreach to broaden a company's customer base.
Lean enterprises typically produce 25% to 50% less scrap and rework with 20% to 50% fewer engineering hours and 25% to 75% fewer factory support hours.Recognizing the social responsibility of reducing waste can lead to long partnerships with other brands committed to similar objectives. By focusing on these ethical practices, startups imbue their product with a deeper narrative that goes beyond mere utility, connecting with consumers on a value-based level.
The Tim Woods theory, therefore, is not just a tool for eliminating waste, but a mechanism to drive strategic growth and sustainability. Experiencing these benefits makes the investment in waste analysis both immediate and far-reaching in its impacts. Identifying, minimizing, and eventually eliminating production wastes stand as pillars that can make or break a startup in this competitive market landscape.
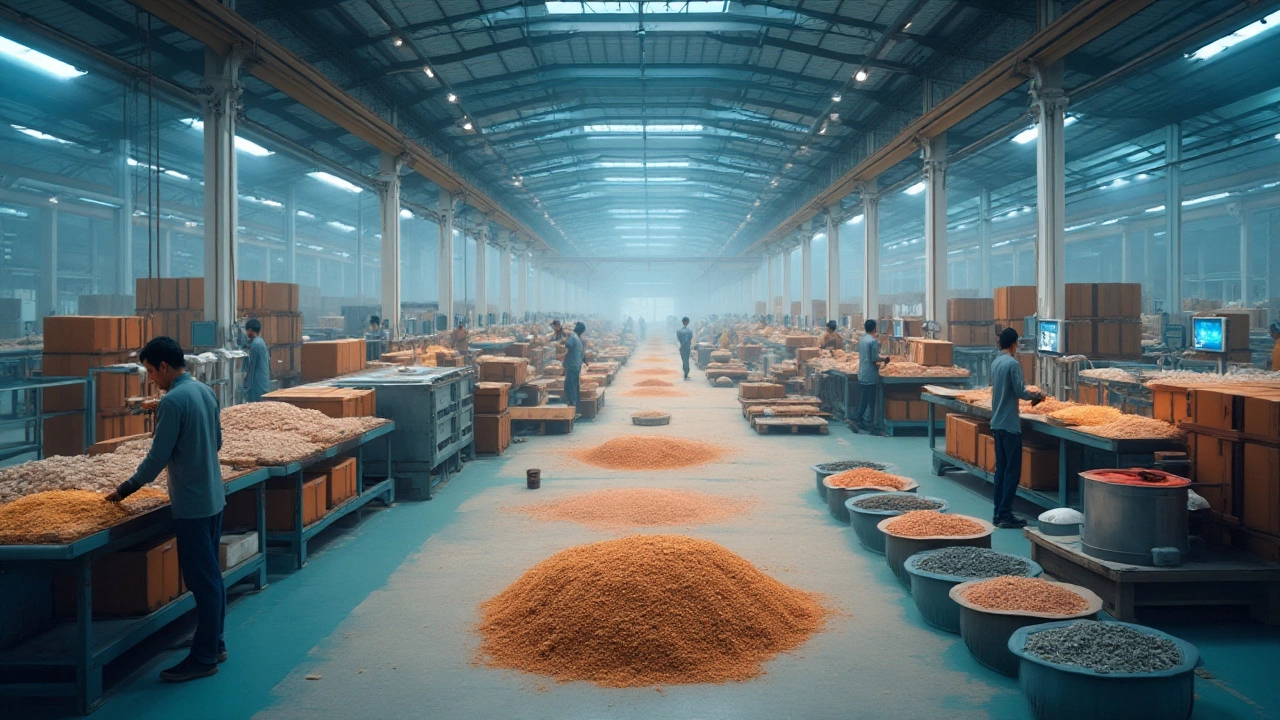
Practical Tips for Success
Creating an efficient manufacturing startup calls for a strategic approach. One key strategy is integrating the Tim Woods theory into your workflow, allowing you to spotlight waste and optimize processes. Identifying these areas creates room for continuous improvement. The first step is education: ensure your team understands the significance of each waste category and sees the direct impact on your manufacturing line's productivity. Training sessions, workshops, and real-world examples can make these concepts more tangible, encouraging a culture of continuous improvement and innovation.
Another vital step is maintaining an open feedback loop. Having open communication channels between different departments encourages collaborations that can uncover areas of waste previously overlooked. Regularly scheduled brainstorming sessions can spark creative solutions to persistent challenges. When team members feel heard, they engage more actively in efforts to adhere to lean manufacturing principles. In fact, expert lean manufacturing advocate Shigeo Shingo once said,
"The most dangerous kind of waste is the waste we do not recognize."This insight emphasizes the need for awareness and constant vigilance.
Next, consider the implementation of simple but effective visual management tools, such as Kanban boards. These tools help effectively manage timelines, tasks, and workflow without being cumbersome. By visually displaying tasks in real-time, you create a streamlined process where everyone is on the same page. Tools like these reduce unnecessary motion and waiting, two critical waste areas under Tim Woods theory. As you start, it's helpful to pilot these methodologies in smaller projects first, gathering team feedback before a wider rollout. Experimentation is key to finding a tailored approach that fits your business needs.
Also, utilize technology to boost efficiency. Technologies like AI and machine learning can analyze processes and identify inefficiencies faster than traditional methods. Incorporating automation in certain areas may also streamline operations and save on labor costs, redirecting focus to more strategic tasks that require human intervention. A survey by Deloitte indicated that 53% of businesses have already started using AI to enhance their productivity.
Technology | Usage Percentage |
---|---|
AI | 53% |
Machine Learning | 39% |
Lastly, always benchmark your processes against industry standards. Comparing your performance metrics with other businesses in the sector lets you measure progress and maintain competitiveness. Business publications often provide insights into benchmarks regarding different metrics. This level of awareness keeps your goals realistic and performance-oriented, ensuring that all efforts employed towards minimizing waste are both effective and efficient. Remember, waste reduction is a journey, not a destination. Each small step taken today sets the stage for greater success tomorrow.