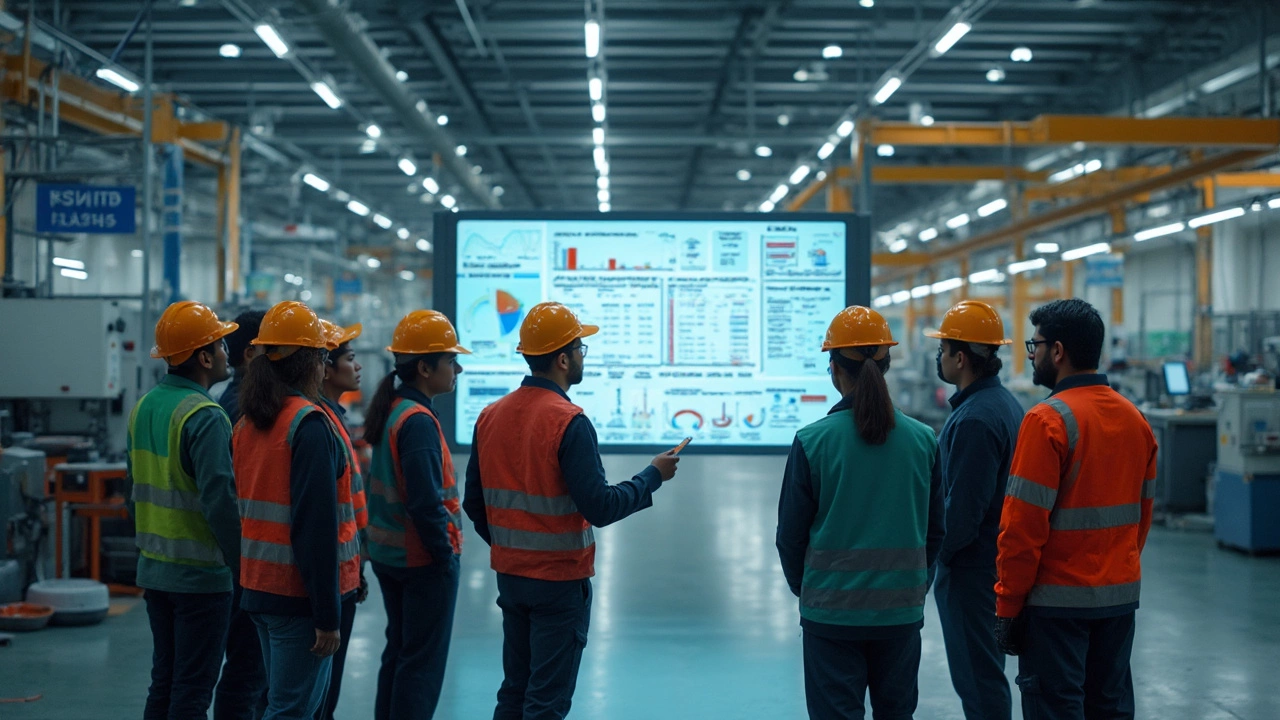
When people talk about manufacturing, it’s easy to get lost in shiny machines and massive factory floors. But to really get results, especially if you’re tapping into government schemes, it all comes down to seven factors. Miss one, and even the best funding won’t save you from headaches down the line.
Here’s something you probably won’t hear at a trade show: A single weak spot in your team, your machines, or even in the raw stuff you buy can wreck your timeline or your budget. Government-backed programs love paperwork, but they love results even more. If you can show strength in every key area, you’re already a step ahead of the crowd.
Want to avoid shutdowns and keep the inspectors happy? Make sure you know what really matters in manufacturing. There’s more at stake than making products – you’re building trust, too. So, what are these seven magic pieces, and why should you actually care? Let’s break it down, so you can skip the fluff and build something strong from the inside out.
- People, Skills, and Teamwork
- Raw Materials and Resources
- Machines, Equipment, and Technology
- Processes, Quality, and Continuous Improvement
People, Skills, and Teamwork
You can have the latest machines and endless capital, but without the right people, your factory won’t run well—or for long. In Indian manufacturing, the Ministry of Skill Development reports that companies investing in worker training see up to a 20% jump in productivity. It’s not just about hiring, but also training, upskilling, and keeping your team motivated through real teamwork.
Having a mix of fresh talent and seasoned experts makes a difference. The best performing factories balance experienced supervisors with young, tech-savvy operators. Here’s what you need to focus on:
- Hire for both technical know-how and a willingness to learn—skills can be taught, but attitude is everything.
- Regular training programs cut accidents and increase output. Big names like Maruti Suzuki run ongoing workshops to keep skills sharp.
- Open communication beats silos. Simple things like daily team huddles or feedback boxes help spot small issues before they become big ones.
- Recognition and small rewards actually boost teamwork and morale. Even basic awards like “employee of the month” get results.
Check the table for a quick look at common results when factories focus on people:
Action | Result |
---|---|
Ongoing Training | Reduced errors by 15%-25% |
Team Meetings | Faster problem-solving, less downtime |
Clear Roles | Higher job satisfaction, lower turnover |
Want to stand out when applying to manufacturing factors grants? Agencies often ask how you’ll support your team. Show you have a game plan for skill-building and solid teamwork, and you’re already halfway there.
Raw Materials and Resources
If you want to keep your production line steady, you need the right materials, and you need them on time. A lot of folks underestimate how tight things can get when your main supplier drops the ball—or if prices suddenly shoot up. Supply chain hiccups have burned even the biggest factories in the last few years, especially during global events like the 2020 lockdowns. According to the Confederation of Indian Industry, raw material costs can make up to 60% of the total manufacturing expenses in certain sectors like textiles and chemicals. If you get this factor wrong, it doesn’t matter how fancy your machines are—the whole system stalls.
Here’s a simple tip: never rely on only one source for important inputs. Government schemes often ask for proof of resource reliability before they approve big grants or contracts. That means you’ll want:
- Multiple suppliers for your key raw materials (think steel, plastics, or electronics)
- Backup plans for shipping delays
- Contracts that lock in prices for at least part of your order, to dodge sudden spikes
Don’t ignore quality, either. Cheap materials can wreck your production stats and lead to a pile of returns, killing both margin and reputation. Make sure suppliers meet the quality standards that government schemes usually set, like BIS (Bureau of Indian Standards) or ISO certifications.
It’s also crucial to track your usage and manage waste. Materials sitting around eat up storage space and cost you monthly, while shortages slow you down. Smart companies use software to monitor inventory, place orders, and even predict shortages before they hit. If you’re a smaller operation, even a good spreadsheet can make a difference.
Material | Average Cost % of Total | Key Supplier Country | Common Risks |
---|---|---|---|
Steel | 35-40% | India, China | Price swings, delivery delays |
Cotton | 50-60% | India, USA | Seasonal shortages |
Plastics | 25-30% | China, UAE | Import restrictions |
Paying attention to manufacturing factors linked to your materials makes your whole business run smoother. Miss this, and you’re stuck with late deliveries, failed audits, or even lost contracts. That’s a cost no company wants.
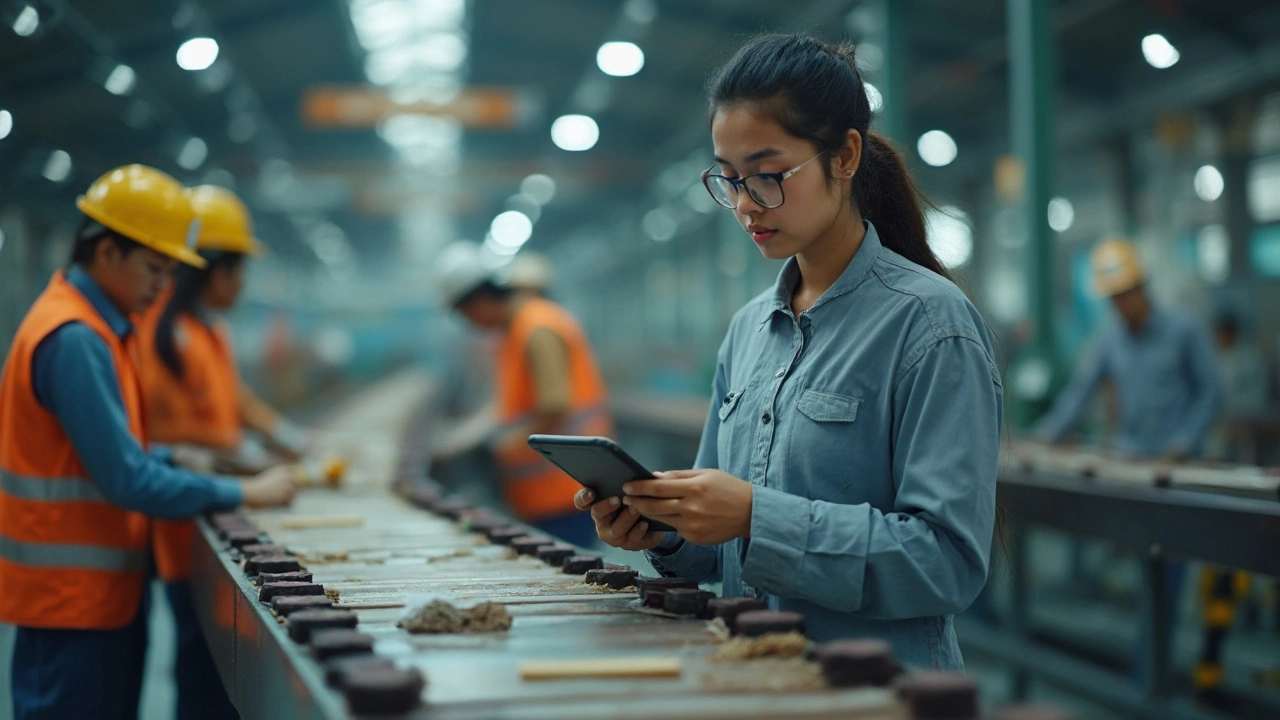
Machines, Equipment, and Technology
If you want your factory running like clockwork, never treat machines as an afterthought. Choosing and maintaining the right gear can make or break your productivity and your ability to tick all the boxes for manufacturing factors in government schemes.
One of the first big questions is: should you buy brand-new machines or stick with older models? New tech often boosts speed, saves energy, and cuts errors. For example, a 2023 survey by the Federation of Indian Chambers of Commerce & Industry (FICCI) found that smart factories, using up-to-date automation, saw a 30% jump in output compared to traditional setups.
But this isn’t just about fancy robots. Even simple upgrades — swapping out worn-out conveyor belts or installing better sensors — can lower downtime and accidents. Want proof? The Ministry of Heavy Industries reported that plants modernizing their equipment under the National Capital Goods Policy improved production efficiency by up to 25% over two years.
Here’s a basic checklist people often overlook when it comes to machines and tech:
- Can your gear handle changes in demand quickly?
- Are the machines energy efficient? (Energy bills skyrocket with old stuff!)
- Is regular maintenance in place? Unexpected breakdowns hurt the bottom line the most.
- Can newer machines upload real-time data, making reporting for government schemes dead simple?
- Are your teams trained for both old and new tech? New machines are wasted if nobody knows how to fix them.
Some factories like automation and robots for repetitive tasks, but others focus on strong, durable machines for bulk production. The sweet spot is finding what fits your product and budget — don’t just chase buzzwords.
Let’s look at some quick numbers. Here’s how updated equipment stacks up against the old stuff in Indian factories:
Factor | Old Equipment | Modern Equipment |
---|---|---|
Average Output (units/day) | 4,000 | 5,200 |
Downtime (hours/month) | 45 | 18 |
Energy Use (kWh/unit) | 1.3 | 0.9 |
Maintenance Cost (per year, ₹) | 2,00,000 | 1,10,000 |
So, when applying for or following a government manufacturing scheme, having solid, tech-forward machines and careful upkeep isn’t a bonus — it’s a must. Expect regular audits. Keep detailed paperwork and inspection records ready. And never forget: the tech is only as good as your team’s ability to use it day in, day out.
Processes, Quality, and Continuous Improvement
Let’s get real—your process is what keeps your factory running or grinding to a halt. Good process design means fewer mistakes, stable output, and less money wasted. In manufacturing, a broken process is usually the root cause when deadlines go sideways or products come out wrong.
Quality control is not just a checklist for inspectors. It’s about catching problems before your customer or a government auditor does. If you’re working under a government scheme, you’ll probably have to follow certain quality standards, like ISO 9001 or the BIS certification in India. These are not just buzzwords—they matter when you want to win contracts or pass scheme audits.
Continuous improvement, or Kaizen as factories in Japan call it, means you’re always looking for a smarter way to work. You don’t wait for a big crisis to fix things; you’re tweaking and updating all the time. Believe it or not, Toyota’s consistent small changes in their methods boosted their productivity by over 10% in just a few years according to their own manufacturing data from the late 2000s.
Here’s a quick table to show what using smarter processes and quality checks can do for manufacturing plants:
Before Continuous Improvement | After Improvement (1 year) |
---|---|
Defect Rate: 8% | Defect Rate: 2.5% |
Production Downtime: 40 hours/month | Production Downtime: 12 hours/month |
Customer Complaints: 36/year | Customer Complaints: 9/year |
If you want actual results, build habits, not just systems. Quick tips:
- Standardize every task—clear steps, no guessing.
- Use data, not gut feeling, to spot and solve process problems. Make charts if you have to.
- Double-check supplier quality before materials even enter your plant.
- Celebrate small wins, like reduced errors, so your team stays invested.
Don’t treat quality control as an afterthought. It’s the difference between being in business next year or scrambling for survival. Treat continuous improvement as job security in a changing world.