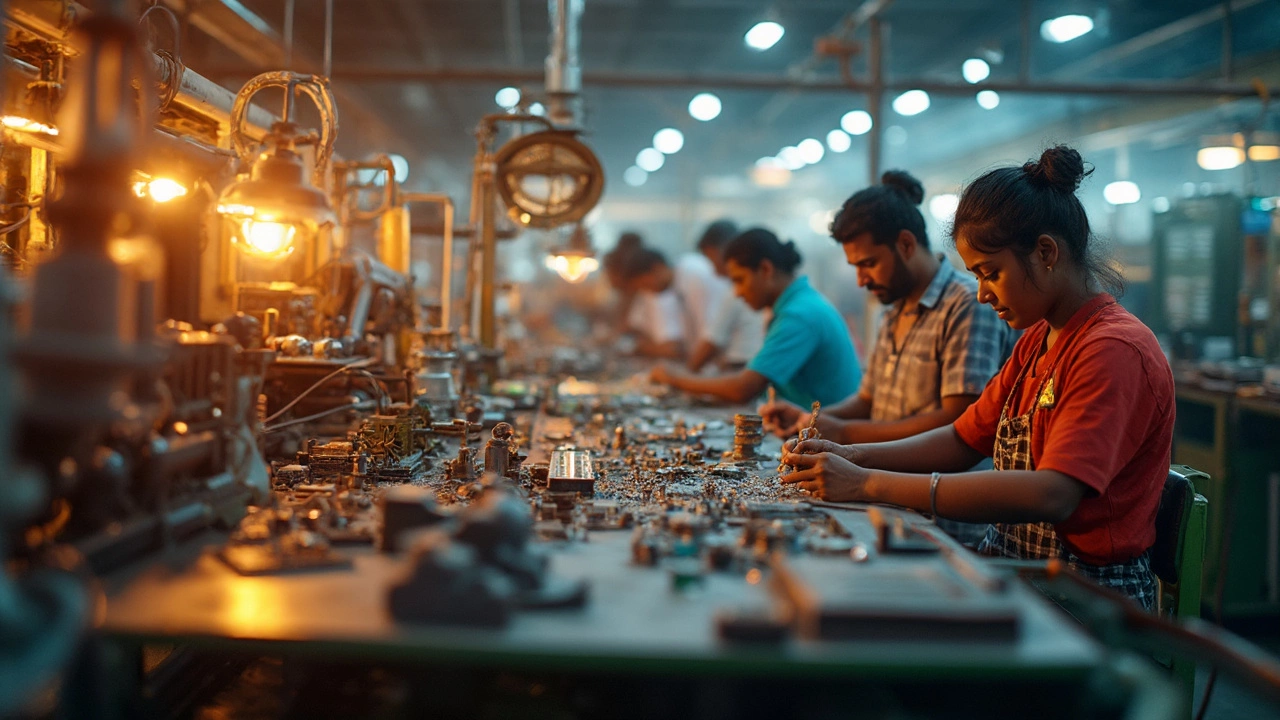
Ever wondered how things get made on a massive scale? When it comes to manufacturing, there are six key processes that cover most of the bases, especially when we talk about government-supported projects. These processes are essential for everything from building cars to crafting tiny computer chips.
First up, we have the assembly line. This process is all about putting everything together, part by part. Think of it like putting together a Lego set, but with way more complexity and automation involved. And it's not just for cars—assembly is crucial in electronics, toys, and even furniture manufacturing.
- Assembly Line Magic
- Fabrication Fundamentals
- Mold Making: Artistic Precision
- Machining: Cutting-Edge Techniques
- Joining Forces: Welding & Beyond
- Additive Manufacturing: The 3D Revolution
Assembly Line Magic
The assembly line is the beating heart of mass production and is a crucial piece in many manufacturing processes supported by government schemes. It’s been around since the early 20th century, thanks to Henry Ford making it famous with the Model T. Today, it’s been tuned and re-tuned to become more efficient than ever.
In an assembly line, products move down a conveyor belt while workers or robots add parts one step at a time. This approach dramatically slashes production time since everything is happening simultaneously rather than sequentially. Imagine this like a relay race, with each station handling a specific task before passing it on.
Core Components
- Conveyor System: The backbone that keeps items moving smoothly across the various assembling stages.
- Workstations: Each task, from welding to testing, has its dedicated spot.
- Quality Control: Key to catching issues before they become bigger problems. Factories often incorporate inspection points throughout the line.
An interesting fact: the modern automotive assembly line can churn out a car every 45 seconds. These lines aren't just fast—they're smart, too. With advancements like computer vision and real-time data monitoring, they ensure that output is as precise as it is quick.
How Government Schemes Enhance the Line
Government schemes often provide the lifeline through funding, infrastructure support, and tax breaks aimed at boosting the efficiency and capacity of these lines. When the government steps in, they often help with the heavy lifting, like upgrading to greener technology or supporting R&D initiatives for new production methods.
What’s exciting is the push towards sustainable manufacturing. New schemes promote the use of eco-friendly materials and energy-efficient practices, making the assembly line a focal point for reducing carbon footprints.
In boosting production methods, the assembly line remains unparalleled in its magic. And with constant improvements and strategic backing, it's likely to stay on the cutting edge for years.
Fabrication Fundamentals
Let's get real about fabrication. In the world of manufacturing, it's about turning raw materials into something useful. Whether it's cutting, bending, or assembling, fabrication is where things start taking shape. It's like magic, but with a lot of heavy machinery.
At its core, fabrication involves techniques like welding, cutting, and assembling metal structures. Think of those massive beams in a skyscraper or the intricate parts of a car chassis. No kidding, our cities and vehicles rely on this process to function.
Common Fabrication Techniques
There are some popular methods involved in the fabrication process:
- Cutting: You can slice through materials using saws, lasers, or plasma cutters, depending on the precision you need.
- Welding: Joining metal parts through heat is a tried-and-true method. It's as much a science as it is an art.
- Bending: This involves manipulating the material into desired angles and shapes. Machines do most of the heavy lifting here.
Each of these methods has its own tools and techniques, and getting them right is key to ensuring quality and efficiency.
Challenges and Innovations
Fabrication isn't without its challenges. The rise in environmental regulations and the demand for more lightweight, durable materials keep pushing the industry to innovate. Luckily, technology has our back. With advanced robotics and new materials, fabrication is more efficient and precise than ever.
If you're thinking of diving into this industry or just curious, remember fabrication is the backbone of industrial processes. It's where raw ideas meet reality.
Technique | Examples | Applications |
---|---|---|
Cutting | Laser cutting, Waterjet | Precision parts, Prototypes |
Welding | MIG, TIG | Construction, Automobiles |
Bending | Press brakes | Chassis, Structural beams |
Mold Making: Artistic Precision
When it comes to manufacturing processes, mold making is like the Michelangelo of the industrial world. This process involves creating a cavity—a mold—that's used to shape materials like plastic, metal, or glass. It's crucial for making everything from car parts to the packaging we encounter daily.
The magic starts with designing a mold, often with the help of computer-aided design (CAD) software. Once the design is finalized, the mold is usually made out of metal and refined to the micrometer using high-precision tools. Accuracy is key here—the slightest mistake can lead to huge costs. That's why skilled craftsmen and women are essential in this field.
Types of Mold Making
There are several types of mold making processes, each serving different purposes. The most common ones you'll find in government-backed manufacturing schemes include:
- Injection Molding: Used to produce everything from bottle caps to large automotive parts. Material is injected into the mold at high pressure.
- Blow Molding: Perfect for making hollow products like plastic bottles. Air pressure is used to form the material against the mold.
- Compression Molding: Involves placing material in an open mold and then pressing it closed. Ideal for creating durable materials.
Quick Facts about Mold Making
Here are some bite-sized facts to chew on:
- The mold making industry is expected to grow significantly, thanks to increased demand for customized products.
- Advanced technologies like 3D printing are starting to play a role, creating prototypes faster than ever before.
- China and Germany are among the leaders in mold manufacturing globally, supplying molds all around the world.
Despite being an old practice, mold making continuously adapts with technological advancements, maintaining its critical role in production methods. Knowing these details can be a game-changer, especially if you're looking to invest or participate in large-scale manufacturing projects.
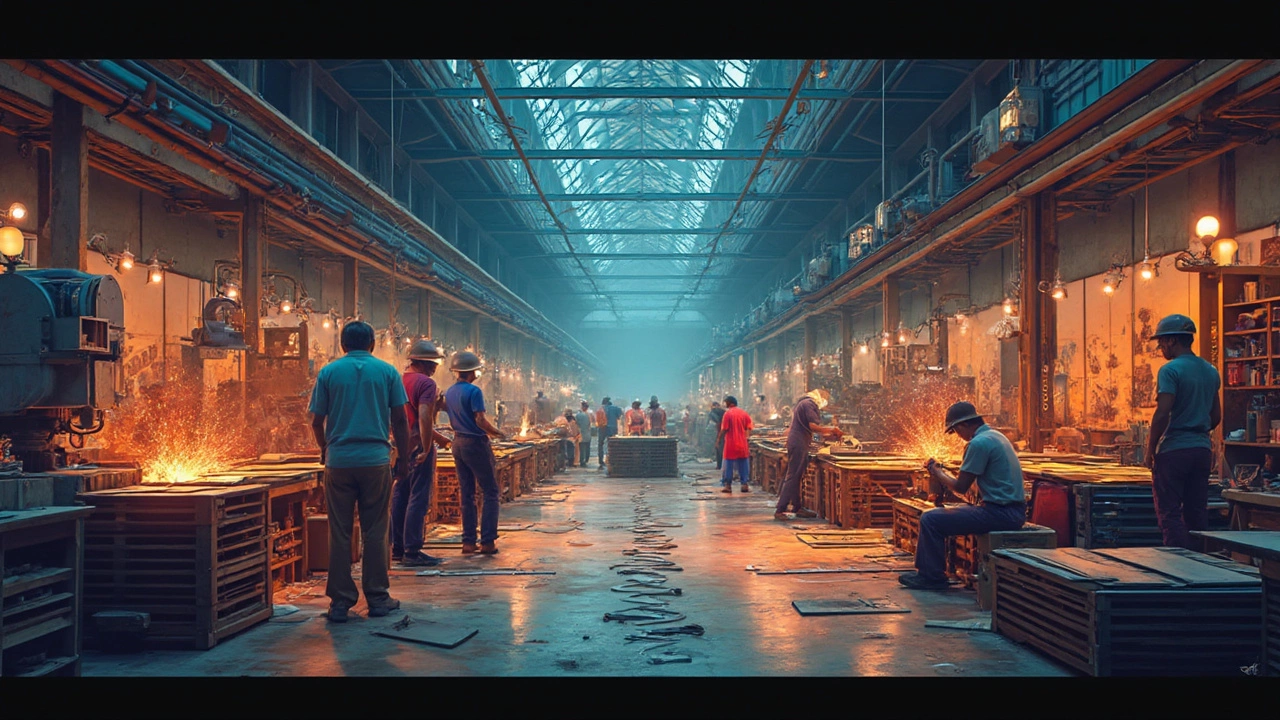
Machining: Cutting-Edge Techniques
Welcome to the world of machining, where precision meets productivity. It’s like sculpting, but way more high-tech. At its core, machining is all about removing excess material from a workpiece to shape it into something useful, typically using drills, lathes, or milling machines.
One traditional method that’s not going anywhere is turning. Picture a hunk of metal spinning like a record while a tool carves away at its surface—that's turning. Another favorite is milling, where rotary cutters chip away material from the piece to create grooves, slots, or complex features. These methods might sound old-school, but they're just as crucial today, especially when paired with computer numerical control (CNC) technology.
Why CNC Machining is a Game-Changer
With CNC machining, we’ve dialed up the precision to a whole new level. It's like the difference between trying to draw a straight line freehand vs. using a ruler. Computers control the intricate movements and speed, resulting in accuracy that a human just can't match.
Industries like aerospace and automotive rely heavily on CNC technology. Why? Imagine making an airplane part. A millimeter off could spell chaos. CNC ensures every component is made to spec, drastically reducing the chances of errors.
Fun Fact: Laser and Waterjet Cutting
Here’s something you might not know: lasers and water jets are becoming popular in machining. They both cut, but without the need for direct mechanical contact. While lasers are great for precision and speed, waterjet cutting is your go-to for cutting heat-sensitive materials like certain plastics or metals.
Technology | Precision | Material Suitability |
---|---|---|
CNC Machining | High | Most metals and plastics |
Laser Cutting | Very High | Thin materials, metals |
Waterjet Cutting | Moderate to High | Heat-sensitive materials |
Choosing the Right Machining Process
So, how do you decide which method to use? It’s all about the job requirements:
- For complex parts with tight tolerances, CNC machining is typically your best bet.
- If you need super-smooth edges or are working with fragile materials, consider waterjet cutting.
- Laser cutting is excellent for speed and efficiency on smaller, detailed projects.
The right choice can save time, reduce waste, and improve overall product quality. As manufacturing techniques evolve, staying updated on these cutting-edge technologies can give any industry an edge—literally and figuratively!
Joining Forces: Welding & Beyond
When it comes to manufacturing, the secret sauce often lies in how different parts are joined together. This is where welding and other joining techniques come into play. You might think welding is just about melting metals together, but it's a bit more intricate than that. Various methods like arc welding, friction stir welding, and even laser welding are used depending on the materials and precision needed.
Welding isn't just about metal either. In industries where plastics and composites are becoming more common, techniques like ultrasonic welding are making headway. And in government-supported manufacturing sectors, the emphasis is often on creating secure and lasting joints to ensure the safety and reliability of products.
Different Welding Techniques
- Arc Welding: This is the most typical method used for fusing metals, employing electricity to create enough heat to melt and join metal parts.
- Friction Stir Welding: A newer method that uses frictional heat to soften and join materials, perfect for softer metals like aluminum.
- Laser Welding: Ideal for high-precision work, often used in electronics and automotive industries.
- Ultrasonic Welding: Used for joining plastics and even electronic components without needing extra adhesives.
Government schemes often support research in these areas to improve efficiency and reduce costs. For instance, according to a 2023 industrial survey, companies that received government grants for welding technology development reported a 20% reduction in manufacturing time and costs.
For manufacturers navigating government schemes, understanding the variety of welding and joining methods available can be the key to better planning and execution of their projects. It not only boosts production efficiency but also ensures products meet necessary safety standards and regulations.
Additive Manufacturing: The 3D Revolution
Welcome to the world of additive manufacturing, or as most of us like to call it, 3D printing. If you've ever been curious about how we can create complex objects with a touch of a button, this is the process to know. Instead of carving away material, additive manufacturing builds products layer by layer, just like constructing a cake tier by tier.
What makes this process so revolutionary? For starters, it's incredibly flexible. Traditional manufacturing methods can be limiting when it comes to design. With 3D printing, intricate designs and unique geometries are game on. This is particularly useful in the healthcare sector where custom-fit solutions—like prosthetics and implants—can be made quickly and precisely.
The Perks of Going Additive
Let's take a closer look at why this technology is catching on fast:
- Reduced Waste: Since material is only added where needed, there's far less waste compared to traditional subtractive methods like machining.
- Speed and Flexibility: Prototyping is super speedy, making it easier for companies to get from concept to model in no time. It's design-on-the-fly.
- Customization Galore: Personalization is the name of the game. Custom products can be made without the need for expensive molds or retooling.
In terms of government schemes, additive manufacturing is being explored for its potential to boost local manufacturing capabilities and diminish reliance on imports. Here’s an example: NASA uses 3D printing to create parts for spacecraft, significantly reducing costs and allowing for greater design freedom.
Jargon Buster: Key Techniques
Within additive manufacturing, a few standout techniques are reshaping industries:
Technique | Application |
---|---|
Stereolithography (SLA) | Dental and jewelry industries thanks to its precision |
Fused Deposition Modeling (FDM) | Common in consumer 3D printers, great for prototypes |
Selective Laser Sintering (SLS) | Used in aerospace and automotive for strong, durable parts |
As this 3D revolution continues, it's turning the traditional manufacturing world on its head, offering promising possibilities for governments and industries alike.